The Next Wave: 3D-Printed Homes
Interview with Kristen Henry
Photos by SQ4D
Kristen Henry, chief technology officer at SQ4D, explains the advantages of 3D-printed home construction for both builders and consumers.
<strong>When and why was SQ4D founded?</strong>
Our CEO, Sal Ferrari, was in construction and owned a lot of real estate properties. He was getting really frustrated with issues like supply-chain disruptions and tenants putting holes in his Sheetrock walls and figured there had to be a better way to build homes. He first created a robotic system to do so but instead shifted to 3D printing, starting SQ4D back in 2017. We’ve since built three homes here in Long Island, including the country’s first legally permitted 3D-printed house.
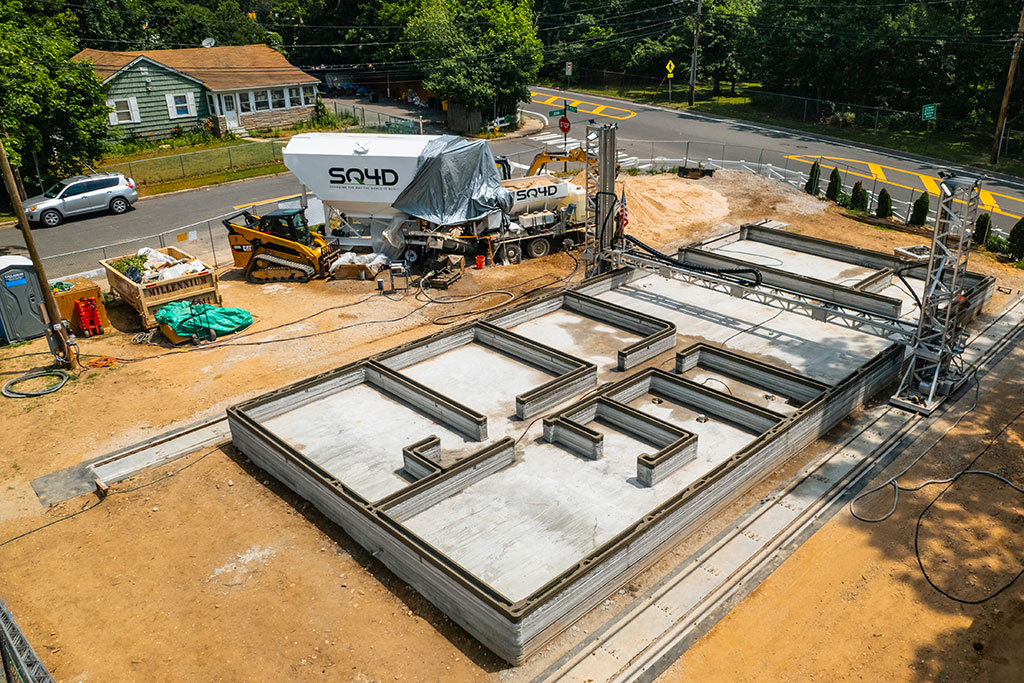
Your company’s tagline is “Changing the way the world is built.” How are you achieving this?
We see our technology as being groundbreaking for residential and commercial real estate and infrastructure. The cost savings compared to traditional construction is a big reason why. For one, we build with concrete, which is cheaper. Two-by-fours are very subject to supply-chain issues and price fluctuations. Concrete is a lot less so, especially since we only use simple, nonproprietary, locally bought materials for it: Portland cement and sand.
Labor costs also go down because we only need a general site worker, a printer operator, and a concrete mixer on-site. Our projects are completed faster as well—in thirty to forty days—and electric and plumbing are incorporated into the process, so construction-site costs are lower.
Finally, the homes created by our 3D-printing technology are built to last. We use 9,000-psi concrete, which has a very high compression strength, and add vertical and horizontal rebar throughout. The homes are essentially fireproof and insect-proof, and you don’t have to worry about flooding or having wood rot. As a result, we include a fifty-year warranty—something that’s pretty unheard of in the industry—and the homeowners will have much lower insurance costs.
How does your 3D-printing process work?
It’s very simple, so whatever an architect can dream up, we can print; for instance, it’s just as easy to create a curved wall as it is a straight one, something that would be very complicated to do via traditional construction. We simply take the 2D architectural plans and turn them into a 3D model that we use to print the house, creating the footings. As we build the interior and exterior walls, we have checkpoints where we pause to add electrical outlets, door and window frames, and countertop switches and outlets. We then continue printing over top of them. We plan to 3D-print roofs soon as well, which will make the structure completely fireproof.
Is this an eco-friendly way of building?
Creating concrete is a carbon-intensive process, but the material is still more eco-friendly than wood in the long term. The life cycle of these homes is a lot longer—we expect them to last centuries—and we’re saving countless trees from being cut down, which will be a net benefit concerning carbon dioxide. In addition, an alarming amount of postconstruction waste ends up in landfills, but with 3D printing, you know exactly how much concrete you need for a house, so there’s no waste.
That being said, there’s potential to get a lot more eco-friendly. One idea we’re looking into is partially or fully replacing the sand in our concrete with glass that otherwise would be destined for landfills.
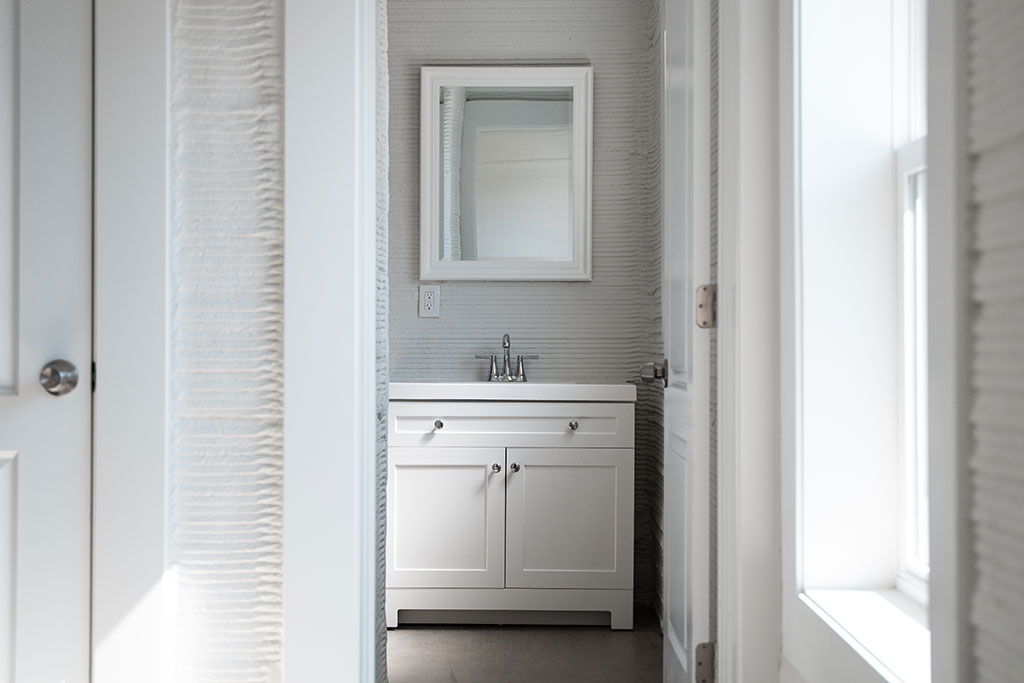
Does your company face skepticism from buyers?
Definitely. As a whole, the construction industry, homeowners, and consumers are rather resistant to change. And despite all the advantages of a 3D-printed home, it still looks different from a traditionally constructed house. We don’t use vinyl siding, for example, and we’ll usually leave the 3D printer’s lines as a statement of sorts (though we can also smooth them out). In America, we’ve been building with wood for hundreds of years, so this reaction isn’t surprising, but across Europe it’s quite conventional, even expected, to use concrete in buildings.
Are there any inherent challenges with concrete, such as cracking?
In general, concrete cracks—that’s just the nature of the material. When it hardens and strengthens, there’s a chemical reaction called hydration, in which the cement reacts with water and forms a chemical bond that gets stronger over a twenty-eight-day period. For that process to happen correctly without forming cracks, the material needs to have sufficient water to hydrate. So we’ve automated our machine to include a misting system that dampens the concrete as it’s printing to make sure the material is curing as well as possible—we just hit a button to adjust the cement-to-water ratio depending on which part of the house we’re doing and the overall weather conditions.
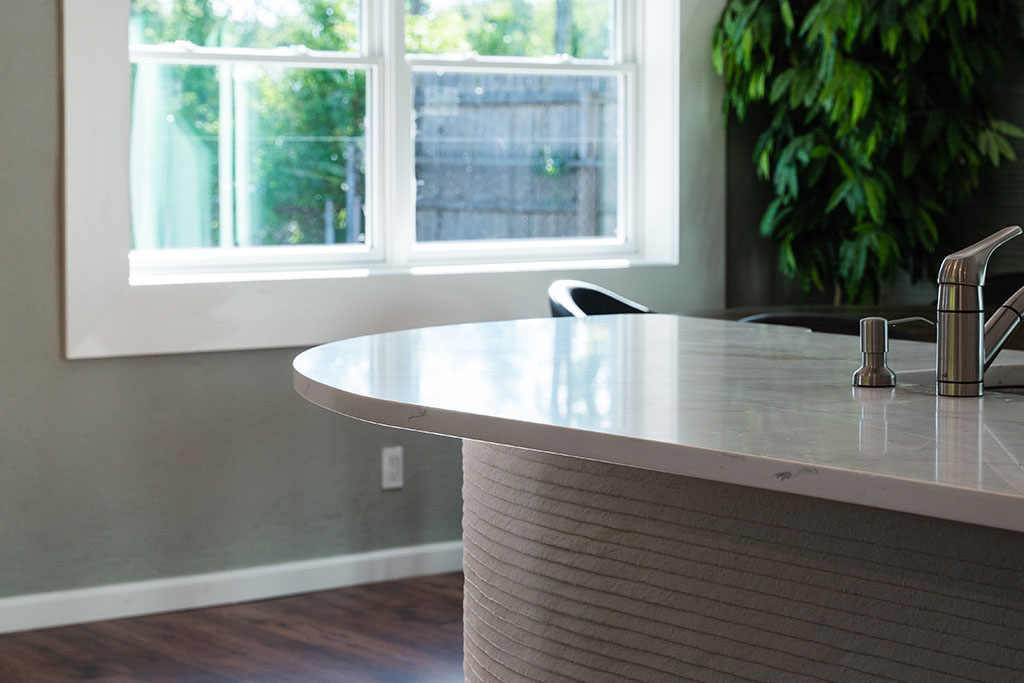
Concrete tends to be cold. Is that a problem with heating and cooling?
Our process actually increases R-value. The walls, on average, are eight inches deep on the exterior and are filled with spray foam, so there’s about twice as much insulation as in a traditional wood-framed home. With the resulting cost savings, we’ve been able to include solar panels on our homes at no additional charge.
How have homeowners responded to their 3D-printed homes?
All of them are very happy in their respective houses. For example, the person who’s living in the Riverhead house really likes the wood floors and warm-colored walls, saying it really feels homey. And the family that moved into our latest home in nearby Islandia has only had positive things to say—other than being a little frustrated because random people keep calling them and showing up to their house wanting to see it. [Laughs] They are also super excited about the solar panels. They actually called us because they didn’t get an electricity bill for the first three months. They thought something was wrong!
What are SQ4D’s goals for the near future?
We are technology specialists more so than construction specialists. By the end of the year, we plan to bring our machines to market across the world so builders everywhere can start reaping the benefits we’ve talked about. We can’t wait to see what they can do with this technology in their hands and are eager to help them make a difference. We think it can be a game changer for both them and people looking for homes.
For more info, visit sq4d.com